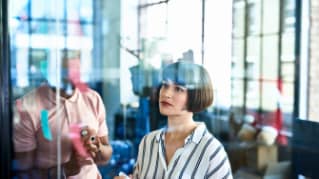
Consumer Markets Hot Topics Webcast - June 2025
Join PwC’s Consumer Markets leaders as they explore the pivotal trends and topics shaping the industry.
Join PwC’s Consumer Markets leaders as they explore the pivotal trends and topics shaping the industry.
Consumer markets assurance insights is a quarterly summary for the consumer markets industry. It provides an overview of emerging economic, accounting, reporting and regulatory matters relevant to the industry.
Southwest used GenAI with PwC to modernize its crew management software—cutting planning time in half, reducing costs and accelerating transformation.
PwC, KAYAK & Blockskye transform corporate travel with blockchain, cutting costs, increasing transparency and streamlining booking.
A workforce reckoning is underway in consumer markets as the labor market experiences transformative shifts.
President Trump's policies and executive orders have significantly expanded the scope of products and countries subject to tariffs impacting the Consumer Products industry.
Companies are steering towards the low end of their long-term growth guidance, but analysts/investors seemed skeptical of those conservative outlooks.
A recap of the operating performance of hotels and sub-market trends, the transactions environment, supply pipeline and more.