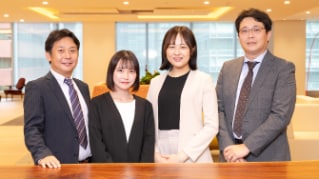
生産領域へのERP導入、PwCの強みとは
製造業界出身で、現在はPwCコンサルティングで製造業を対象としたERP導入を手掛けるディレクター佐田桂之介と、シニアマネージャー尾中隆喜が、基幹システムを導入する際のシステムの「標準化」の意義や克服すべき課題について語ります。
基幹システムの導入には業務やシステムの「標準化」が欠かせません。しかし、日本企業、とりわけ製造業には独特の生産思想や商習慣、業務体系や人事制度が深く根付いているため、標準化が極めて難しいとされています。PwCではいかにしてそのハードルを乗り越え、製造業へのERP導入を実現しているのでしょうか。製造業界出身で、現在はPwCコンサルティングで製造業を対象としたERP導入を手掛けるコンサルタント2名と、若手アソシエイトが語り合いました。
登場者
PwCコンサルティング合同会社
ディレクター 佐田 桂之介
シニアマネージャー 尾中 隆喜
リード
アソシエイト M.I.
アソシエイト A.T.
※法人名、役職、インタビューの内容などは掲載当時のものです。
(左から)佐田 桂之介、M.I.、A.T.、尾中 隆喜
A.T.:日本の製造業界は他の業界に比べてERPの導入が難しいといわれていますが、どのような背景・事情があるのでしょうか。
尾中:まず、日本の製造業は、生産現場で日々の改善活動を積み重ねて競争力を維持・向上させ続けたことによって、世界に誇る生産思想・方式を確立してきた経緯があり、現在もそれが競争力の源泉となっています。しかし、その改善活動が個々の製品や工場ごとに別々に行われてきたために、システムの観点から見ると社内で複数のシステムや複雑なロジックが乱立しているケースが少なくありません。ERPを導入するにはこれらのシステムやロジックを標準化する必要がありますが、それをすることで独自性=競争力が失われるのではないかという懸念が、標準化の足かせになることもあります。
M.I.:生産品目ごとのシステムやロジックの乱立は、日本の製造業特有の課題なのでしょうか。海外のERP導入において同様の課題は見られないのでしょうか。
尾中:全ての国が同じというわけではないですが、例えば日本同様に製造業に強みをもつドイツでは、優れた技術を標準化、ルール化して、誰がやっても同じようにできるような仕組みを作ることが重視されます。一方、日本では「町工場の〇〇さんしか作れない部品」のような、職人技が大切にされます。どちらが正解というわけではなく、単に日本と海外ではものづくりに対する美学が異なるということです。ただ、この違いを標準化という視点から見た場合、日本の製造業の業務体系は海外に比べて多くの課題を抱えていると言えると思います。
特に半導体やレアメタルのような、供給制約を受けやすい部材を扱っている場合、生産に関するデータの分断は経営判断の遅れや失敗を招きます。限られた部材を使って収益を最大化するには、各部材の在庫をどの拠点にどのくらい保有しているかというデータをリアルタイムで把握した上で、生産地の適正化や部材の適正配分を行う必要があるためです。グローバルで生産データをつないだ上で最適化検討と投資判断を行い、その後の投資評価に向け、生産拠点や工場における管理指標といった経営指標との連携が強く求められるようになっているのです。平たく言うと、今どこに在庫がどのくらいあるのかを把握した上で、「どの拠点でどのくらいの人やコストを使って製造すれば、どのくらいの収益が上がるのか」が瞬時に理解できるように各拠点のあらゆるデータを一元化して、経営指標と結び付けておくことが大切だということです。
A.T.:経営指標と各拠点のデータを結びつける上で、日本企業はどのような課題を抱えているのでしょうか。
佐田:従来の日本の製造業では、経営層が工場長に工場経営を一任するケースが一般的でした。良い結果を出している工場長には相応の発言権や裁量が与えられ、KPIに関しても経営層が細かい設定をするのではなく、工場長に委ねられてきました。したがって、複数の工場を持つ企業内では工場ごとに異なる文化が育まれ、各工場独自の生産方式や原価管理が行われてきました。これまでの経営指標は比較的、単純で大まかだったので、それで何とかなっていましたが、昨今、経営側のシステム化が進み、全社経営をしようという機運が高まっているので、各工場にKPIを含め細かい数字を求める傾向になっています。すると「ちゃんと結果を出しているのだから、これまで通りでいいだろう」と細かい数字を提出することに反感を抱く工場長も出てきます。数字が出たとしても、工場ごとに基準が異なることも珍しくありません。例えば「売上原価」を求めても、工場ごとにその定義(何を売上原価に含めるのかの基準)が異なることもあります。そうなると経営層としては、どの数字を信じればいいのかわからず、正しい判断ができません。だからこそ標準化とERPの導入が喫緊の課題となっているわけですが、各現場には「今までうまくいっているのに、なぜやり方を変えなければいけないのか」という反発もあり、なかなか標準化が進まないというジレンマを抱えている企業が多くみられます。
PwCコンサルティング合同会社 ディレクター 佐田 桂之介
M.I.:経営層と現場との温度差がある中で、PwCコンサルティングではどのように標準化とERP導入を進めているのでしょうか。
佐田:ERP導入には、業務改革が不可欠です。また、業務改革を推進する上ではチェンジマネジメントが非常に重要なカギとなります。さらに、チェンジマネジメントの成功には経営層だけでなく、現場を巻き込んだ業務改革のための意識が必要となってきます。システムを勝手に導入して現場に押し付けてしまうと、土壇場になって業務を変えられないといった反発が生まれやすくなります。その結果、使えないシステム、もしくは現行業務の要件を満たすために多大なコストを使ってERP上に作りこみを行うということになりかねません。ERP導入は、IT部門が単独で進めるのではなく、経営層や業務部門と一丸となって進めていくことが大切です。そのためにも、チェンジマネジメントが重要なポイントとなります。
尾中:日本の製造業は特に、先ほどの工場長の話もそうですが、ボトムアップで業務を遂行してきた企業が多いので、いきなり現場の方に「経営側がこう言っているから、やってくれ」とトップダウンで指示をしてもうまくいきません。経営が求めることとは別に、現場が本当に困っていることや求めていることを理解して整理し、ゴールを示すことが大切です。その上で、標準化によって得られることと失われることのバランスを見せて、「標準化により失うものはあるが、この課題は解決できる」と説明し、現場に納得してもらいます。こういった整理をプロジェクトのごく初期の段階で行っておくことが、極めて重要です。
A.T.:経営層と現場とで、課題感がまったく異なっている場合はどうすればいいのでしょうか。
佐田:その企業にとっての強みは何かという議論を深めることが大切です。その議論の中で経営層と現場が「これだけは譲れない」という「強み」について合意ができたら、その部分は無理に標準化せず、アドオン化して残すという判断をする企業も少なくありません。逆にいうと、絶対に標準化したくない「強み」さえ両者の間で共有できていれば、残りは全部標準化しても問題ないという話に持っていけるということです。
尾中:そうですね。よく聞くのは、取引先との関係上、標準化できないという話です。「この商品はある特定のお客様のために特別な作り方で作っている。だから、絶対に譲れない」というものです。社内の問題だけではなく、社外との関係性から標準化できないということです。このあたりの話も、現場の人としっかりコミュニケーションを取ってプロジェクトの初期の段階で把握しておくことが大切です。
PwCコンサルティング合同会社 シニアマネージャー 尾中 隆喜
M.I.:現場の方々とコミュニケーションを深めるコツはありますか。
尾中:なかなか一筋縄ではいきませんが、現場のキーパーソンとなる方と認識の共有ができると、一気に話が進むことが多いです。早い段階でキーパーソンの方とコミュニケーションし、標準化の意義をしっかり理解・納得してもらえるかどうかで、その後の展開が随分違ってきます。では、どうすればキーパーソンを「味方」にできるかというと、やはり現場に入ることです。現場に入って業務をしっかり理解する。その上で現場にとっての標準化のメリットをしっかり訴求します。現場を知らない状態で、突然「コンサルタントです。この現場を標準化しましょう」と言っても、相手の心を動かすことはできません。
A.T.:ERPのメリットについては、どのように説明していますか。
佐田:ERPのメリットは端的に言うと、SCMと会計の領域(財務会計と管理会計)とを連携させられる点で、つまりモノとお金がバラバラに管理されるのを防げるということです。モノは見えるがお金は見えないという状況を防ぐには、ERPは非常に有効なツールだと思います。もちろん、集めたデータをどう活用するのかという別の課題もありますが、一つのシステムの中にモノとお金のデータを集めて一元管理できるという点で、ERPは非常に有効だと思います。
尾中:データ活用については、最近、生産計画や生産管理などの部署の方々からご相談を受けることが多く、実際に生産領域でのAI活用や実証実験、実用化も進み始めています。例えば生産現場では、外観検査や生産ラインの保守・保全に、計画系の領域では外部データを活用した生産ロケーションの適正化や供給リスク分析などにAIが活用されています。ただ、その多くはPoCを通した技術検証であり、生産現場の特定の工程など限定的な範囲での活用にとどまっていて、部門や機能をまたぐバリューチェーン全体での実用にはまだ至っていません。なぜなら、複雑なロジックを解く技術は進歩しているものの、そこに流し込むデータの質や量が不十分であるため、期待した手応えが得られないからです。生産領域でのAI活用には生産準備段階における工程/設備設計情報が重要であり、生産現場の実績値だけでは十分とは言えません。例えば、その製品の工程はどの程度自動化されていて、人の作業はどの程度必要なのか、工場内での部品/製品の動線はどうなっているのか、あるいは置き場などのスペースに余裕はあるのかどうか、といった工程ごとの情報が把握できて初めて、デジタル技術が生きてくるのです。
M.I.:工程設計から生産計画・実行までをデータでつなぐことが大切だということですね。
尾中:そうです。ERPだけで考えるのではなく、PLM-ERP-MESと基盤全体をどう設計し、そこで管理するデータをどう標準化していくのかという視点が非常に重要になります。特にエンジニアリングチェーンの領域では、製品によって仕事の流れが異なることが珍しくないので、データの視点で何を統合・標準化するのか、何を特有なものとして分散・独自を許容するのかを描いた上で取り組むことが、業務標準化成功のカギとなります。
PwCコンサルティング合同会社 アソシエイト M.I.
A.T.:AIの活用にせよERP導入にせよ、業務とデータが標準化されていないと意味がないということですね。
尾中:そうですね。ただし、何から何まで全て標準化すればいいというわけでは決してありません。データの使い道に応じて標準化するか否かを判断し、標準化のツールとしてERPやPLMといったシステムを使い分けて改革を進めることが大切なのではないでしょうか。標準化する業務としない業務の見極めはとても難しいですが、これは企業の強みを見極めることなので、避けては通れない議論です。逆にこの議論を抜かしてプロジェクトを進めてしまうとERP導入の目的を見失いがちです。ERP導入によって自分たちは何をしたいのかを明確化する意味でも、標準化する業務・しない業務の判断は非常に重要です。また、生産現場の要求を全てERPでカバーしようとするのも、避けた方がよいでしょう。ERP上での作り込みが必要になって、導入コストも運用コストも高くなってしまい、上手な使い方とはいえません。
M.I.:ERPのような基幹システムで開発すべき範囲と、周辺システムでカバーすべき範囲があるということですね。どうやって見分ければ良いのでしょうか。
尾中:見極めるためには、ERPで対応できることを正しく理解する必要があります、例えば、「ERPでの生産の表し方=製造指図でのロット生産」と思い込んで、そのまま導入すると生産現場とシステムの間で大きな乖離が生まれてしまいます。
佐田:システムの機能配置も大きな課題ですね。そもそも、日本企業におけるシステム導入は業務を回すための仕組みというよりも、作業を楽にしたり、効率化したりすることを目的としていたため、小回りが利くことを重視した仕様になっていて、基幹システムに必要のない機能も多いのです。そういった機能をERPに持ち込んでしまうと、標準機能で対応できなかったり、アドオンが大量に発生したりしてしまいます。これを防ぐためにも、基幹システムに持ち込むべきデータを見極め、システムの機能配置を決定することが大切です。
A.T.:持ち込むデータの見極めには、どのような点が重要ですか。
佐田:まず、標準化されたデータである必要があります。ただ、中にはERPを入れること自体が目的になり、KPIの再設定や経営層の合意、適切なデータの取捨選択などがなされないまま、小手先でERPを導入してしまうケースがあります。すると本来やりたかったことができなかったり、改修が必要になったりする状況が起こり、最悪の場合は、過去の負債を抱えた新システムを構築し、それを何年も使い続けなくてはならないという残念な結果になりかねません。特に日本では海外に比べて、「システム=自分の仕事が楽になるもの」という発想があり、「自分の代わりをしてくれないシステム=悪いシステム」という考えに陥りがちです。結果としてアドオンが大量に増えてしまい、失敗するケースもあります。
PwCコンサルティング合同会社 アソシエイト A.T.
M.I.:そういった事態を避けるためにも、まずはERP導入プロジェクトの意義を関係者にしっかり周知することが大切だと思いますが、どのように取り組んでいますか。
佐田:これはチェンマネの基本でもあるのですが、まずはスタート時にプロジェクトの大枠の目的を経営層としっかりすり合わせておくことです。それを今度は部長⇒課長⇒現場と共有していくのですが、いきなり私たちのような外部の人間が言ってもあまり効果がないので、クライアント側の社内の上司⇒部下の関係性の中で伝えてもらいます。上司が部下に自分の言葉で説明し、「よし、やるぞ」と声をかけてくれると、部下の皆さんは動いてくれるものです。あとは、先ほどの話にもあったように、キーマンを見つけることです。基幹システムに限らず、何かを「変える」には多くのエネルギーが必要で、リスクもありますが、それを乗り越えるパワーの持ち主を見つけることが大切です。
尾中:本当にそうですね。加えて、飴と鞭でいうところの「飴」をちゃんと用意しておくことも大切です。現場にとって基幹システムの導入は「鞭」が多い業務なので、なかなか積極的に動いてくれません。分かりやすくいうと、例えば「システムに導入で人員が不要になって、自分がクビになるかもしれない」と思わせてしまうと、動いてくれません。そうではなく、「これまで古くて使いにくいシステムを使ってこなしていたルーチンワークも、これからはRPAのような最新ツールを使ってスマートな仕事になる」といった未来や期待感を「飴」として共有して、腹落ちしてもらった上で進めることが大切です。
A.T.:さまざまな課題がある中で、製造業へのERP導入においてPwCにはどのようなケイパビリティがあるのでしょうか。
佐田:PwCコンサルティングは繰り返し生産型のSAPテンプレートを持っており、これを活用して標準化を推進できる点に優位性があります。ただし、このテンプレートを全ての企業にそのまま使ってもらうということではなく、あくまでもこのテンプレートをベースにすることで、標準化をスムーズに推進できるという意味です。また、チェンマネのプロジェクト実績が豊富な点もPwCの強みの一つです。先ほど、チェンマネは経営層の理解を得た上で、ITと業務の両輪で行うべきと言いましたが、その経験・実績も豊富です。さらに、ホームページで紹介しているとおり、特殊業務とされる自動車産業向けJIS/JITの領域についても業界固有のテンプレートを持っており、複数の企業に提案をしています。引き続き、これらの強みを活かして日本の製造業における機関システムの刷新を後押しするとともに、今後は、DSCMとしてPLM/MESの連携領域において最新技術を活用した取り組みにも力を入れていきたいと考えています。
M.I.:貴重なお話をありがとうございました。私は入社以来、SAP導入支援に従事してきましたが、製造業界を担当した経験がないので、大変勉強になりました。また、プロジェクトにおいても「理解を得る」ことが大切であるということを、改めて実感しました。今後の業務に生かして、私もERP導入推進に貢献していきたいと思います。
製造業界出身で、現在はPwCコンサルティングで製造業を対象としたERP導入を手掛けるディレクター佐田桂之介と、シニアマネージャー尾中隆喜が、基幹システムを導入する際のシステムの「標準化」の意義や克服すべき課題について語ります。
SAPの導入は企業の規模が大きくなるほど難しくなるとされています。長年数々の大規模プロジェクトに携わってきたEnterprise Transformation部門のパートナーと若手アソシエイトが、プロジェクトを成功に導くためのポイントについて議論しました。
「2027年問題」が迫るなか、多くの企業は業務改革とシステム再構築の連動という課題に直面しています。Enterprise Transformation部門のパートナー 蔵方玲臣と若手アソシエイトがシステム導入のチェンジマネジメントについて語り合いました。
デジタル化による定型業務の効率化という範疇を超え、新たな価値提供による企業競争力アップに資するDXを実現するポイントはどこにあるのか、会計領域のコンサルタントとして企業変革を支援してきたパートナー望月誠治が語りました。